Bringing up the rear.
So you've already seen that I intend to stuff a Vanagon transaxle into my little Ghia, but the bastardization is far from finished. To transmit massive torque from motor to wheel there are several links to consider. Downstream of the transmission gears are the axle half-shafts, constant velocity joints, and stub axles (in other words, the "axle" part of transaxle). The inner and outer CV joints of a Type 1 VW (Bug and Ghia) are reliable at design loads, but could spew bearings faster than a Navy navigator on Sodium Pentothal if subjected to 300 foot-pounds of torque. Besides, the Vanagon used larger CV joints than my little Ghia came with, so something larger is needed to match things up. Duh, use Vanagon parts, right? Well, turns out there's more to this story. With joint-jolting torque propelling an overweight Ghia to illegal velocities, brake components become critical. No way would I trust my tushie to the skinny rear drum brakes that came as stock, so let's get some vented disks. Besides, we want beefier CV joints and axles. CV options are nicely laid out at Blind Chicken Racing. Oh yeah, if all this stronger stuff came in a lighter package, that would be nice too. Sound like an impossible order? Not if you consider the dynamic duo of VW and Porsche. Porsche has aways done a lot of the big-brain engineering for VW, and would naturally not waste that work when it came to building their own cars. It turns out that Porsche 924 and 944 cars have essentially the same rear suspension type as late model Karmann Ghias! Plus, the 924 and 944 models up through 1986 had a narrow track, using trailing arms of the same dimension as Type 1 Volkswagens. However, these arms used the beefier Type IV (411 and 412 station wagon) CV joints. The Type IV joints share a common diameter and bolt pattern with the Type II bus joints, but they have a greater range of motion. Since I've considered airbagging the Ghia, this is a welcome bonus. What about the brakes? Porsche uses only the best, so the 924/944 line came with vented rear disks and an integrated parking brake. Ok, so this sounds heavy. Yeah, the 944 trailing arms were beefy steel to support a heavier, higher performance car, until 1986, that is. In 1986, Porsche produced a one-year-only narrow track, forged aluminum trailing arm. For yet another bonus, these arms are compatible with the 944 Turbo (951) four piston Brembo calipers, or the earlier two piston calipers. Since I'm trying to avoid boosted brakes for reasons of mass, bulk, and complexity on an electric car, only the early calipers would do.
Long story short, I locally located the rear end of a 1986 Porsche 944 Turbo and a set of early calipers. For properly balanced braking, I pulled a master cylinder from the same, and it turns out that once separated from it's booster unit, the master cylinder 'looks' like it will be a perfect match for the Type 1 mount, only in aluminum instead of cast iron, and properly portioned for rear disks without the need for an external proportioning valve.
Before you get too impressed by my intellect, be assured that it's been figured out by much better mechanics than me. I was particularly inspired by the work of Germany's Jochen Bader, who stuffed the internals of a Porsche 993 into his Ghia, and used much of this rear suspension setup. A good article on the project can be found at http://www.bader-racing.de/en/presse/volksworld.pdf
Our last link in motor-transmission-axle-brake rotor chain is of course, the wheels and tires. Tires are a fairly forgiving component, as evidenced by any number of roadgoing monstrocities these days, from rice racers with their 13"x13" rims and rubber-band tires, to the 35" mud grips found climbing curbs at any suburban shopping center. For the Karmann Eclectric, we want to find a balance between traction and efficiency, style and substance, while keeping it within the wheelwells of my narrow-waisted Ghia, allowing unassisted steering, stock speedometer ratios, and the many other benefits retained through generally staying true to what those Porsche engineers spent so much time figuring out. The perfect compromise may well be 6"x 15" rims from the front end of 1987 924S LeMans Special Edition models. Not only are these rims the right size, with the right offset, and the right bolt pattern, but the Porsche Phone Dial design is of timeless simplicity, with oval holes that smartly complement the Ghia lines. Of course, my local Porsche parts scrounger happened to have a bargain on four of these....
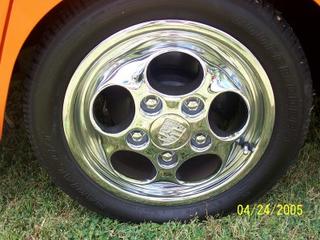
More details to come on the technical specificalities that were glossed over in this post.